Case Study
BHP EP6
Client
BHP
Location
Olympic Dam, SA
Project Dates
2020-2022
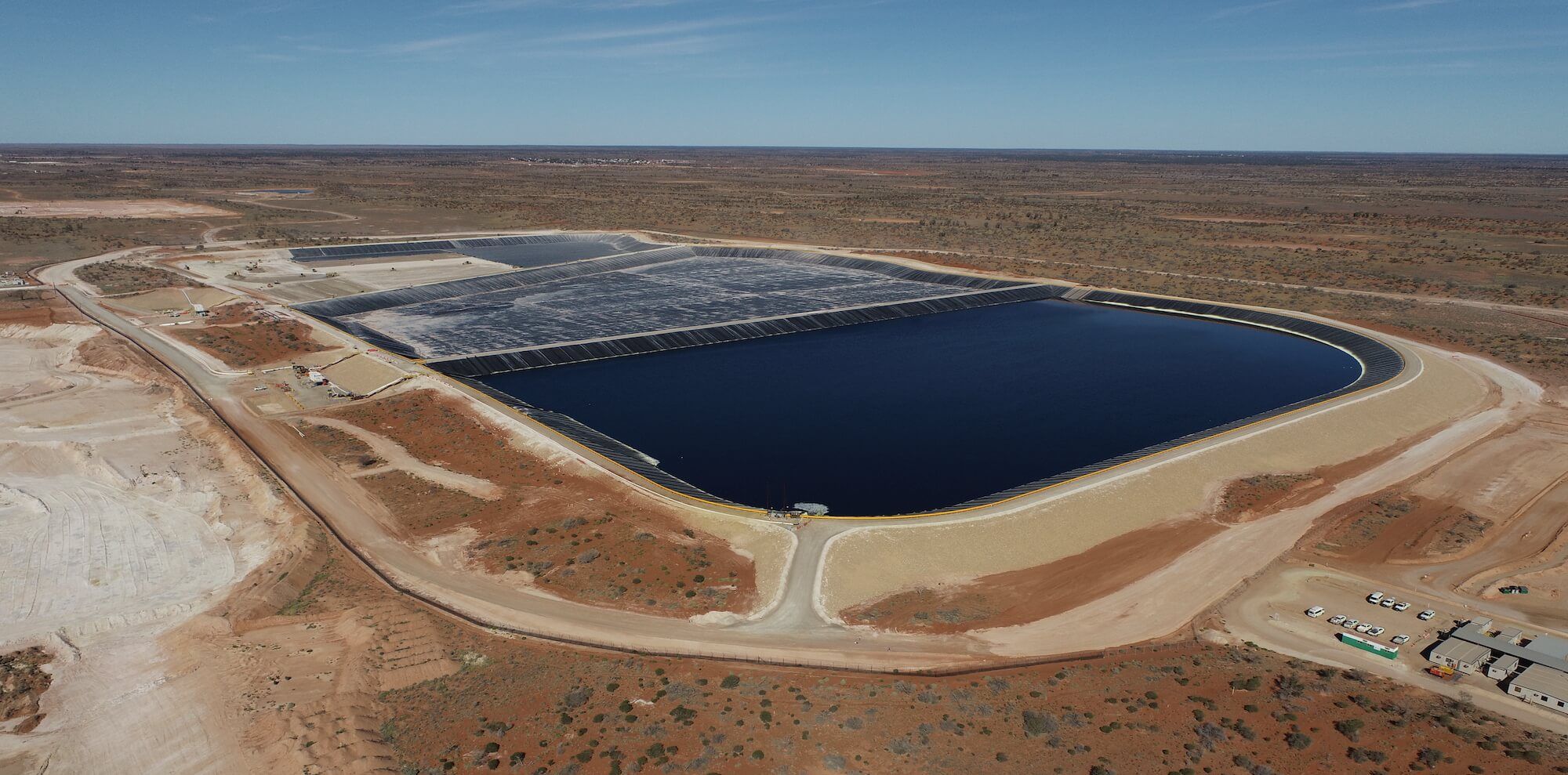
The Challenge
BHP was facing a critical challenge in ensuring the quality and integrity of a custom high-temperature HDPE (High Density Polyethylene) material for their EP6 project. The vast scale of the operation demanded a stringent quality assurance process from the point of manufacture through to the final installation. There was a substantial risk associated with potential defects or inadequacies in the material that could lead to future failures, environmental issues and significant financial repercussions.
Our Solution
To mitigate these risks, GeoQ implemented a two-tiered quality assurance strategy. Initially, GeoQ executed an in-factory audit and closely monitored the manufacturing of the custom high-temperature HDPE to ensure it met all specified standards before its shipment to Australia. This pre-emptive measure was critical in ensuring that the material quality was preserved from the very beginning. Following the successful audit, GeoQ provided comprehensive Electrical Leak Detection services, utilising the latest arc testing technology. This service was performed directly for the civil contractor during the entire geosynthetic installation phase, ensuring that any possible defects were identified and rectified immediately, thus maintaining the highest standard of installation quality.
The Result
The proactive approach taken by GeoQ ensured that BHP’s EP6 project was executed flawlessly, with over 600,000 square meters of HDPE tested and verified for integrity and quality. As a result, BHP benefitted from a significant reduction in risk of environmental harm and potential future financial costs due to material failure, underscoring the value of GeoQ’s expert quality assurance and leak detection services in large-scale industrial projects.
- Conducted pre-shipment in-factory HDPE quality audit
- Verified 600,000m² of HDPE, minimising risk of material failure