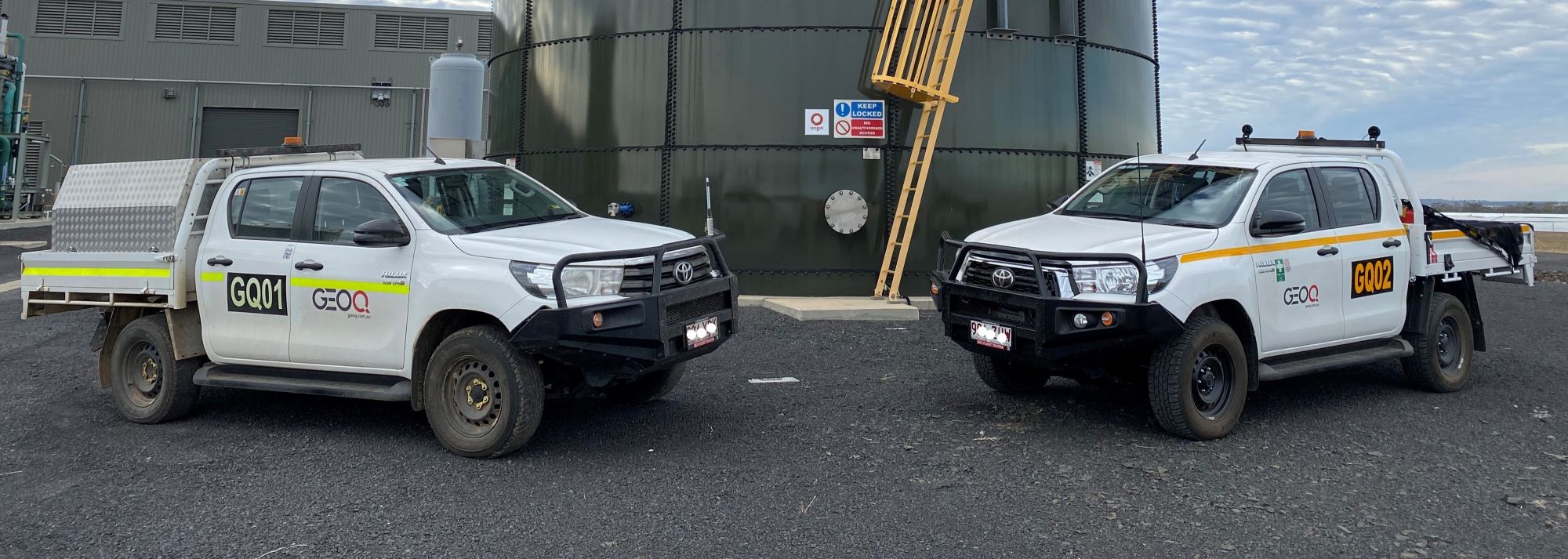
GeoQ Services
Our suite of services extends from Construction Quality Assurance (CQA) supervision to specialised electrical leak detection, emphasising meticulous, third-party assessments of geosynthetic installations. Our objective is to guarantee the integrity and durability of containment facilities, all the while safeguarding Australia’s distinct environment and aiding industries in realising their sustainability ambitions.
Beyond CQA, we offer our expertise in material laboratory testing, ensuring all construction materials satisfy the required specifications and we provide contractor CQC services to support effective project management and compliance. Partnering with GeoQ means securing a commitment to accuracy, dependability and exceptional environmental management.
At GeoQ, we provide comprehensive geosynthetic services, ensuring that every project meets the highest standards of quality and environmental safety.

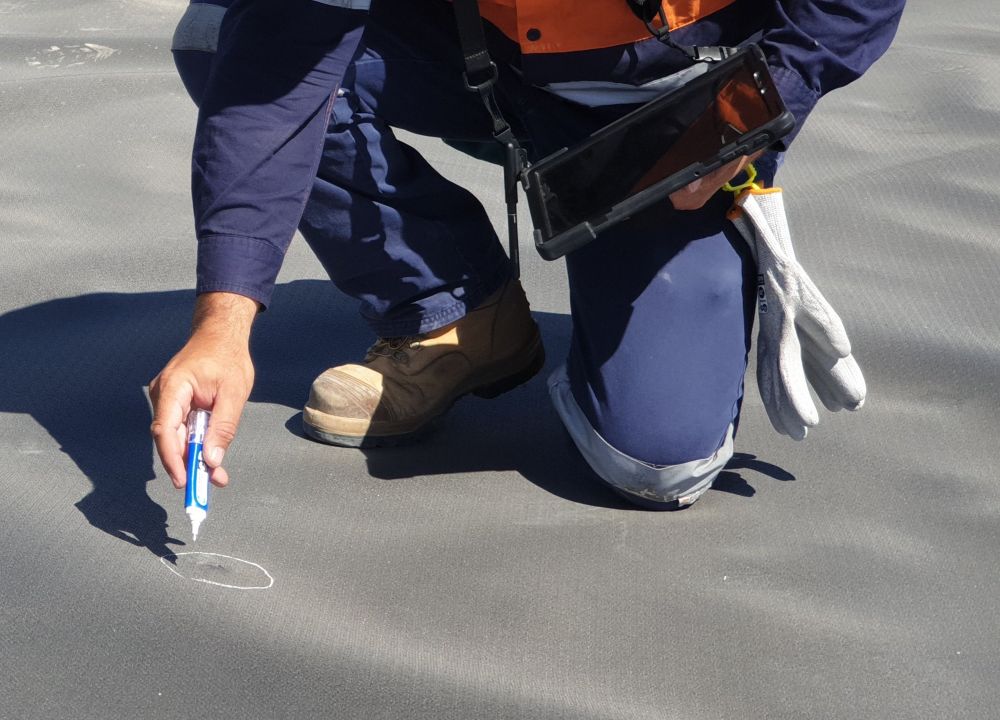
CQA Services
GeoQ delivers excellence with an average of 2 million square meters of geosynthetics tested annually over the past five years—precision, reliability and scale you can trust. Our seasoned team offers comprehensive supervision across various complex geosynthetic systems, backed by international GCI-ICP qualifications, instilling client confidence in the adherence to both project specifications and global standards. With the capability to cater to diverse project scopes both nationally and internationally, GeoQ ensures that Quality Assurance is meticulously integrated, forming the cornerstone of every successful construction project.
- Our inspectors are GCI-ICP certified, ensuring compliance with international geosynthetic standards.
- We offer comprehensive, project-based geosynthetic CQA solutions across Australia and abroad.
- We are dedicated to integrating Quality Assurance as a pivotal component of construction success.
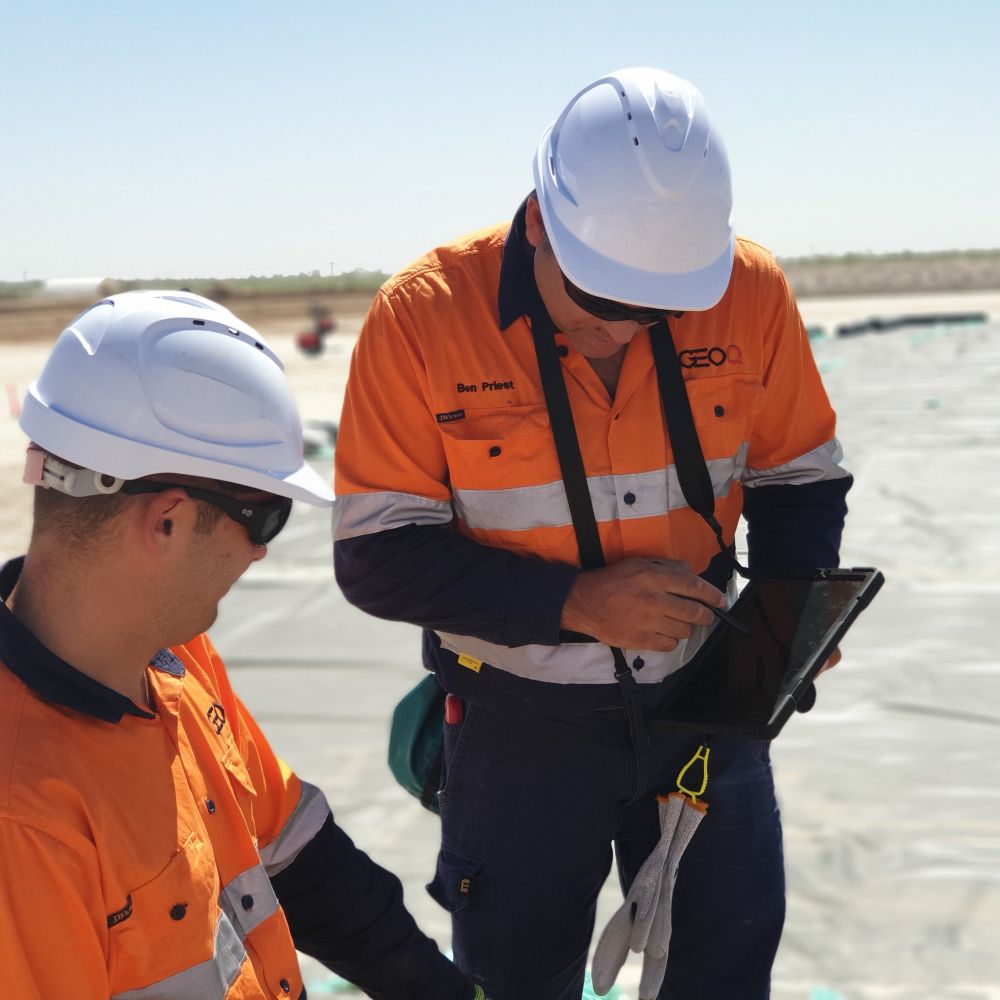
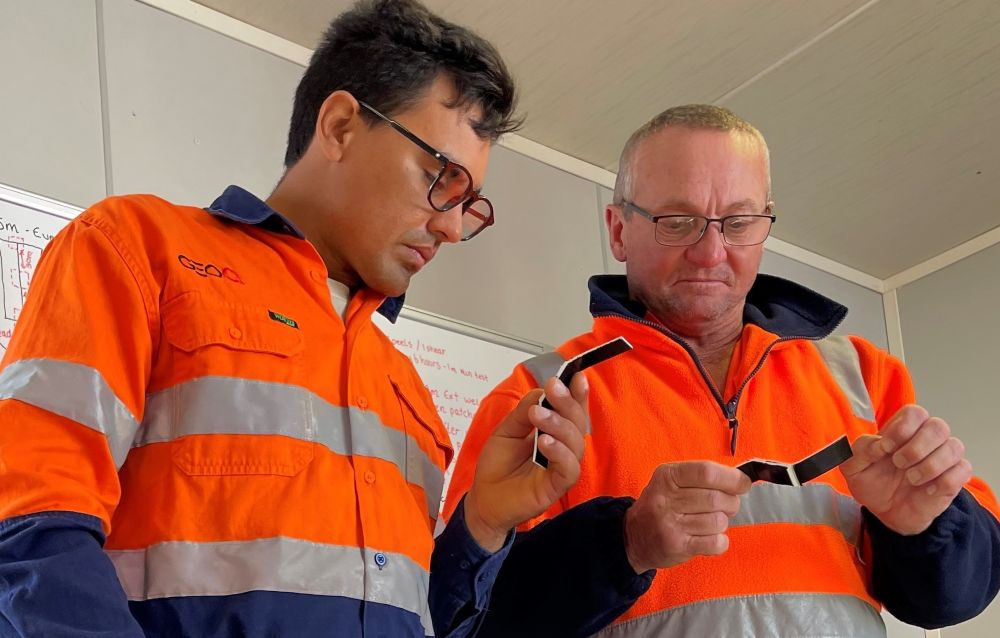
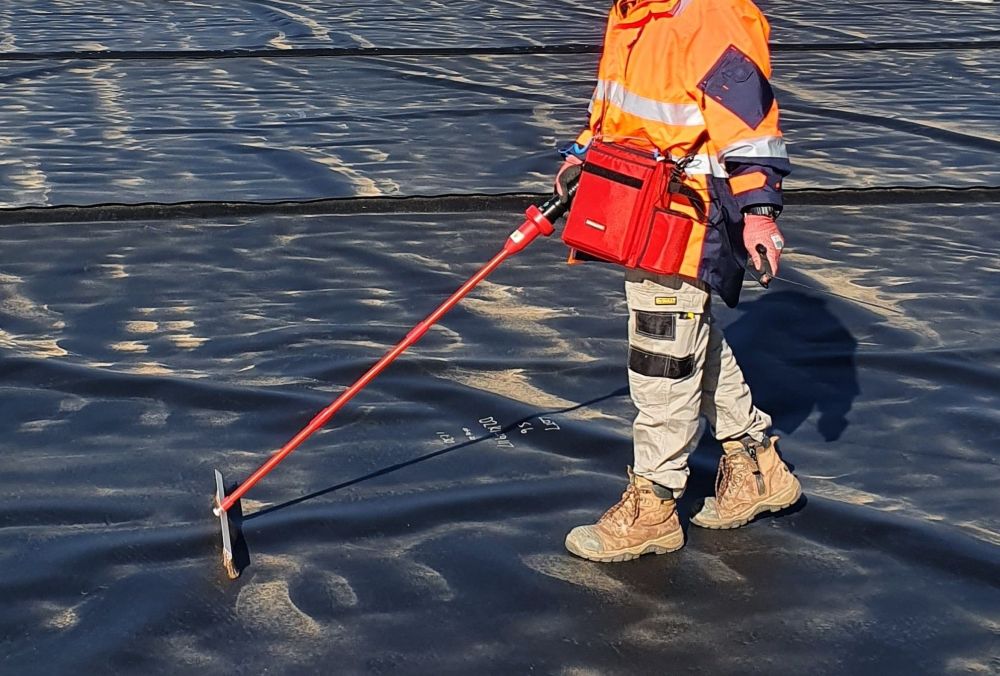
Electrical Leak Detection
GeoQ is a leader in Electrical Leak Detection, using up-to-date technology from global manufacturers, ensuring we remain at the forefront of the industry. Our expert team conducts a full spectrum of electrical leak detection in strict accordance with internationally recognised ASTM standards, including ASTM D6747-15 and D7703-2016. We deliver meticulous reports pinpointing defects with millimetre accuracy and provide visual data representations, leveraging the latest analysis software to ensure comprehensive insights into the integrity of geosynthetic installations.
- We utilise state-of-the-art Electrical Leak Detection equipment for precise assessments.
- We adhere to ASTM standards for rigorous, accurate testing and reporting.
- We are capable of providing services across Australia and internationally, with detailed visual data analysis.
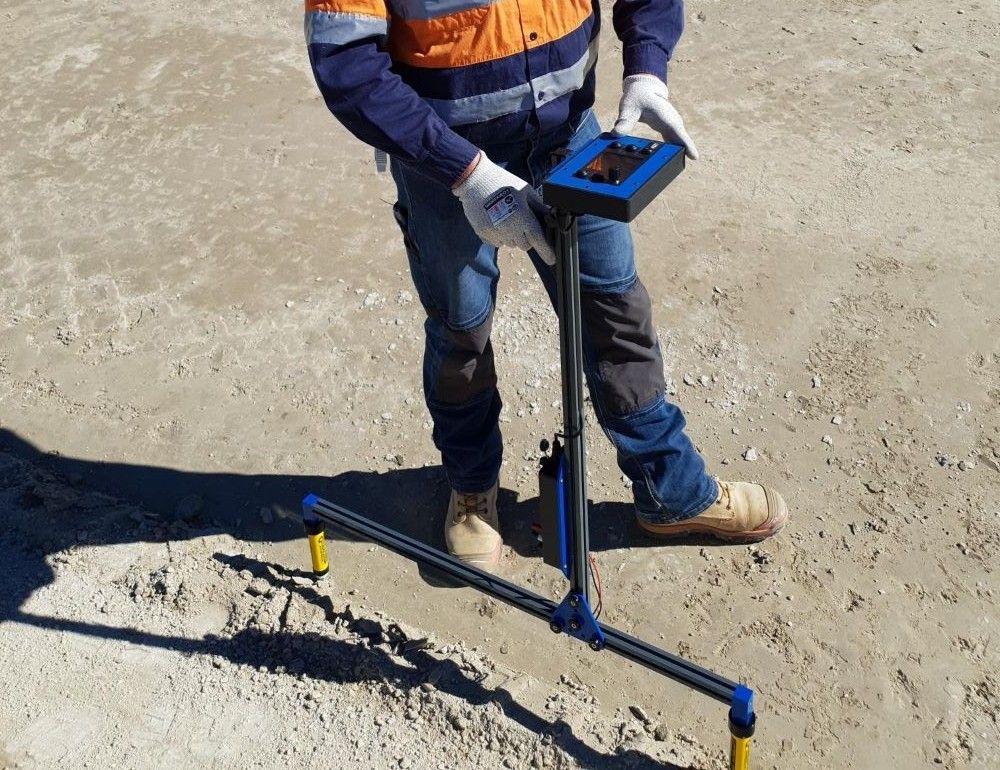
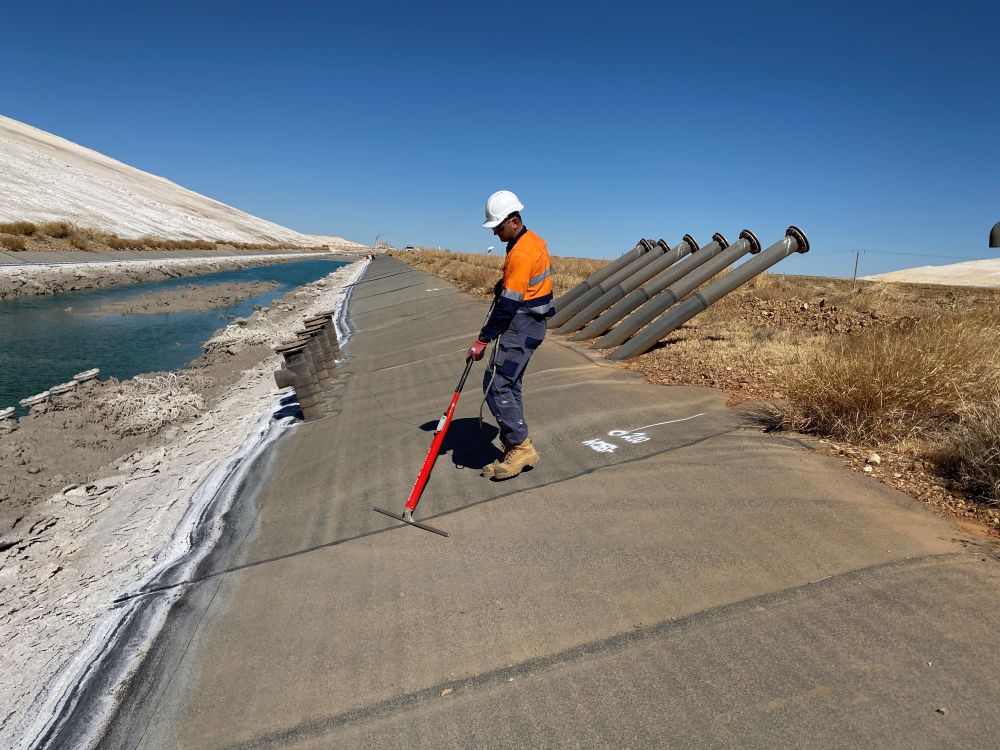
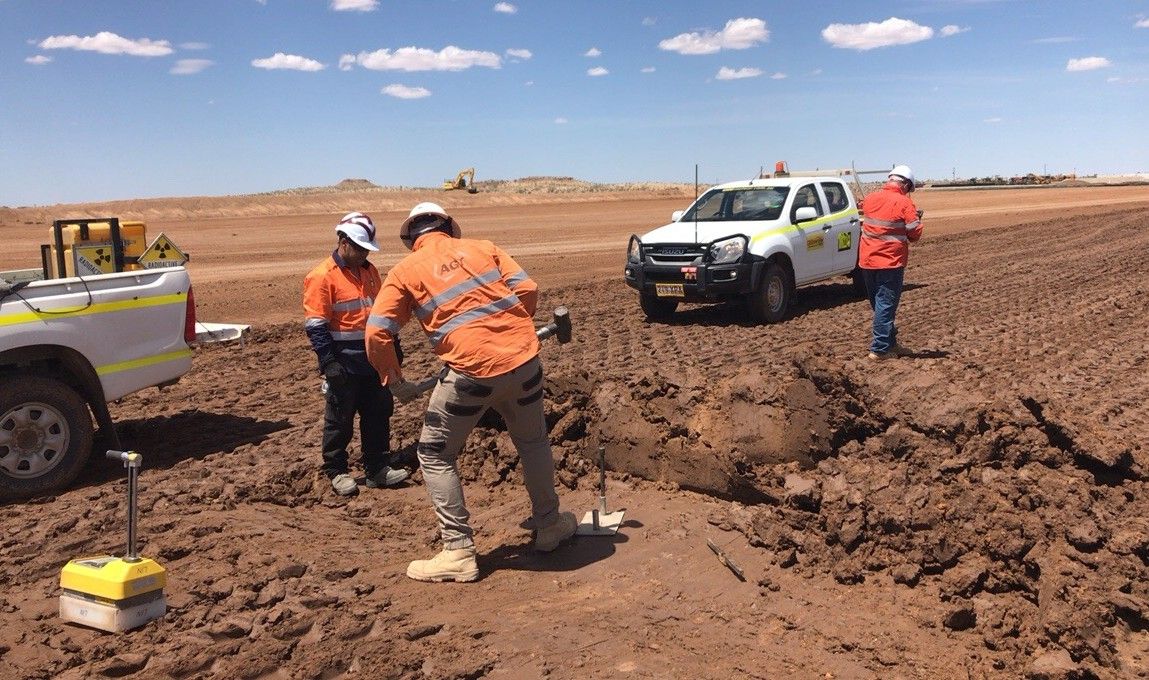
Geotechnical CQA
GeoQ offers comprehensive Geotechnical CQA services, coordinating earthwork material sampling and testing through a network of trusted NATA accredited laboratories. Our qualified engineers and GCI-ICP certified inspectors provide a robust range of Earthworks CQA monitoring services, ensuring the highest quality standards. With GeoQ’s expertise, clients can be confident that their projects will meet stringent industry benchmarks.
- We coordinate sampling and testing with NATA accredited laboratories nationwide.
- We facilitate on-site NATA accredited confirmative and destructive testing labs, ensuring same day turn around on reporting results.
- We offer expert CQA monitoring services by GCI-ICP certified inspectors.
- We meet high-quality standards through meticulous engineering oversight.
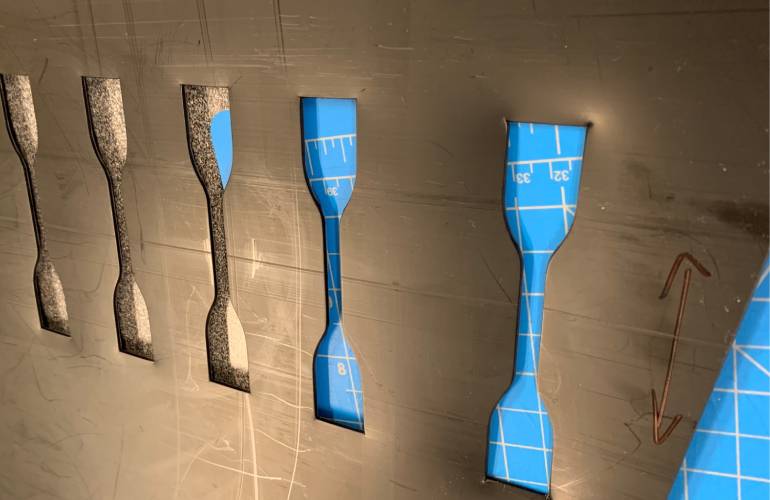
Material Laboratory Testing
GeoQ provides essential material laboratory testing services, ensuring geosynthetic material quality from onsite sampling to independent conformance verification. Our meticulous chain of custody management and use of trusted NATA and GAI-LAP accredited labs guarantee adherence to Australian, ASTM and GRI-GM standards. For international procurement and in-plant sampling, our tailored solutions prevent non-conformances, safeguarding project integrity from production to deployment.
- We facilitate on-site sampling and stringent chain of custody for geosynthetic materials.
- We coordinate conformance testing through accredited labs to meet comprehensive international standards.
- We conduct proactive in-factory audits and sampling to ensure material quality prior to shipment.
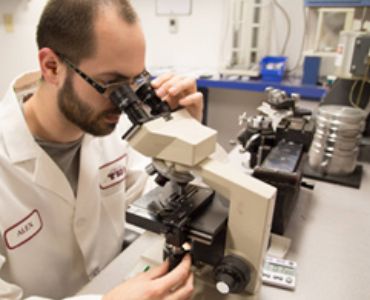
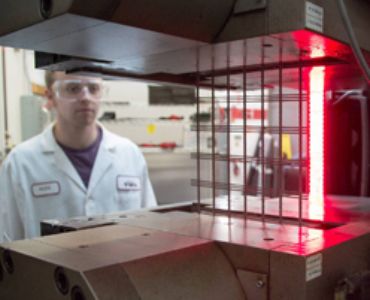
Geosynthetic Liner Repairs
GeoQ offers comprehensive onsite repair services for HDPE, LLDPE and LDPE liners, ensuring integrity and longevity of geosynthetic installations. With our certified International Association of Geosynthetic Installers (IAGI) technicians, we provide efficient and cost-effective repair solutions, along with annual inspections for early damage detection. These inspections, essential for environmental monitoring, can be reported for compliance with EPA standards.
- We offer onsite repair services for all HDPE, LLDPE and LDPE liner defects.
- Our certified IAGI technicians deliver quality repairs and routine infrastructure inspections.
- Our detailed third-party reporting is suitable for environmental compliance and EPA monitoring.
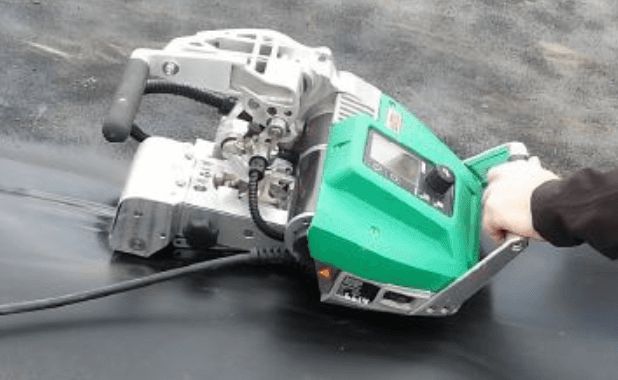
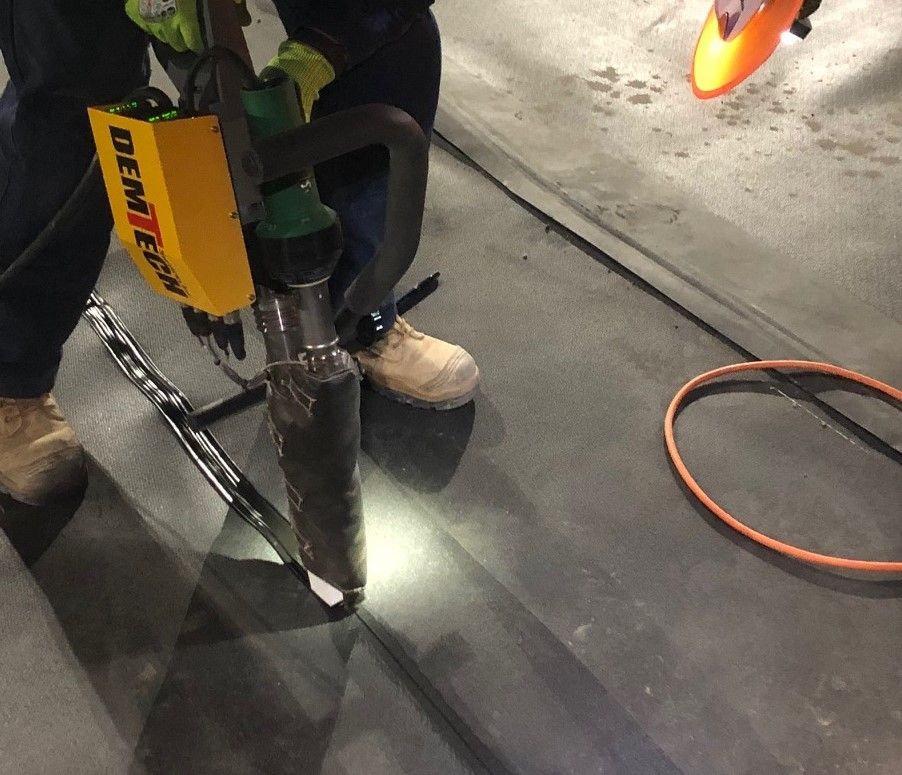
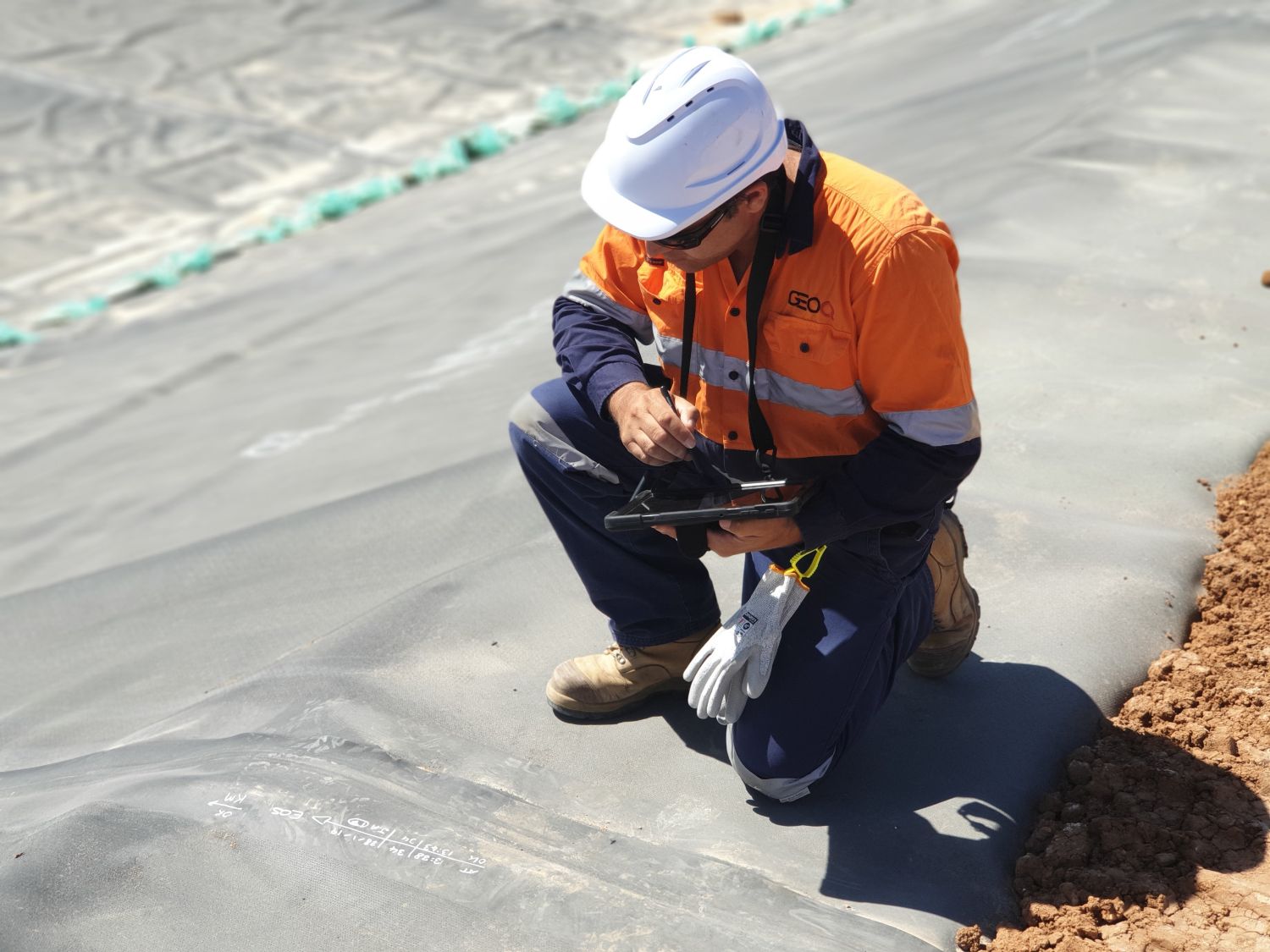
Contractor CQC Services
GeoQ provides comprehensive Geosynthetic Construction Quality Control (CQC) services, catering specifically to installers and contractors who require meticulous CQC data collection and adherence monitoring for project technical specifications. Our customised service offerings include turnkey solutions for Quality Assurance Master Document Register (MDR) submissions, ensuring all geosynthetic and earthworks installations meet the highest standards. With a track record of delivering precise Surveyed Geosynthetic As-built records and detailed installation data, GeoQ ensures seamless CQC submissions throughout the project lifecycle to sustain client trust and project integrity.
- We offer specialised CQC services for geosynthetic and earthworks project compliance.
- We develop tailored turnkey Quality Assurance MDR submissions.
- We progressively deliver Surveyed Geosynthetic Asbuilt records that align with installation data.
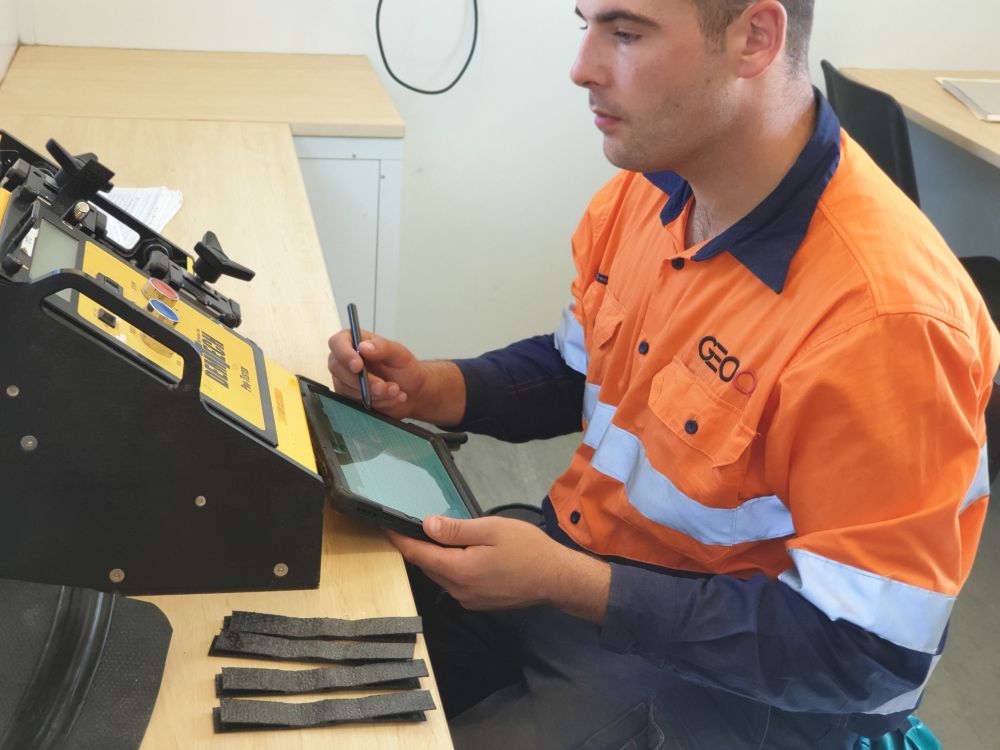
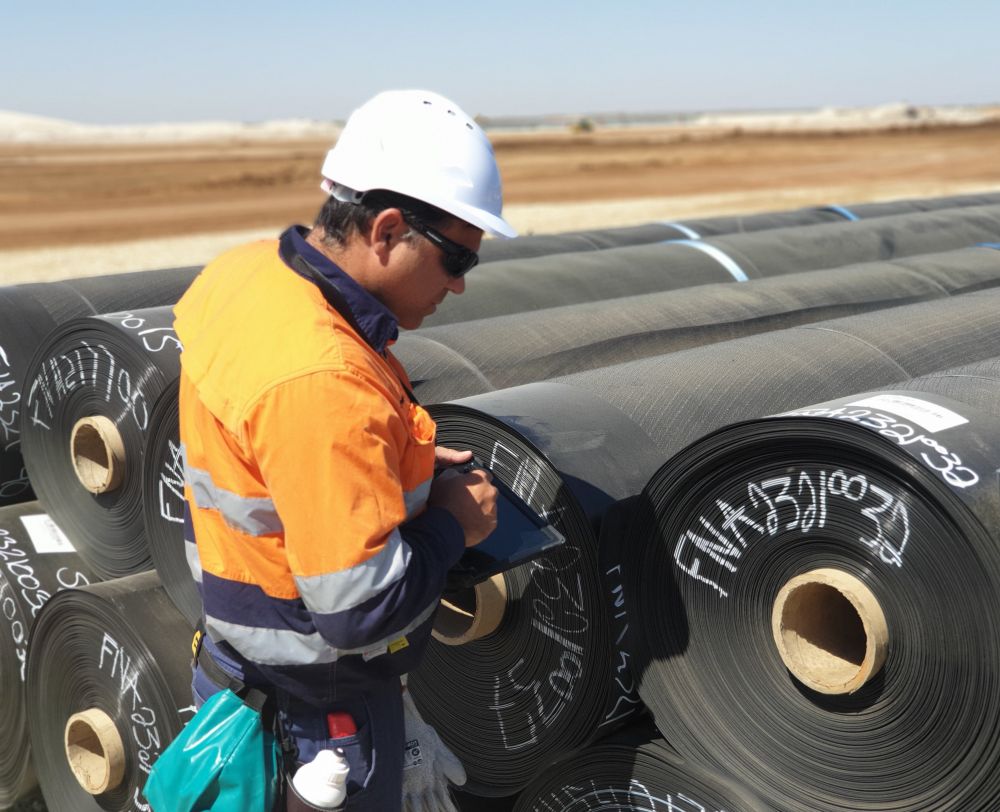
Environmental Solutions
GeoQ is at the forefront of providing integrated environmental solutions, working in partnership with a network of respected engineering design firms, leading international manufacturers, specialist contractors and global industry authorities. We pride ourselves on offering impartial advice tailored to each project’s specific environmental containment needs, ensuring that every client receives trustworthy and expert guidance. Our core principle of dedicated customer service means we’re equipped to assist across a spectrum of sectors including landfill waste, agriculture, oil and gas, metalliferous mining, waste/water storage and biogas industries.
- We partner with renowned engineering and environmental experts for comprehensive containment solutions.
- We offer unbiased, expert advice for diverse environmental projects and industries.
- We are committed to excellent service across landfill, agriculture, energy, mining and waste management sectors.

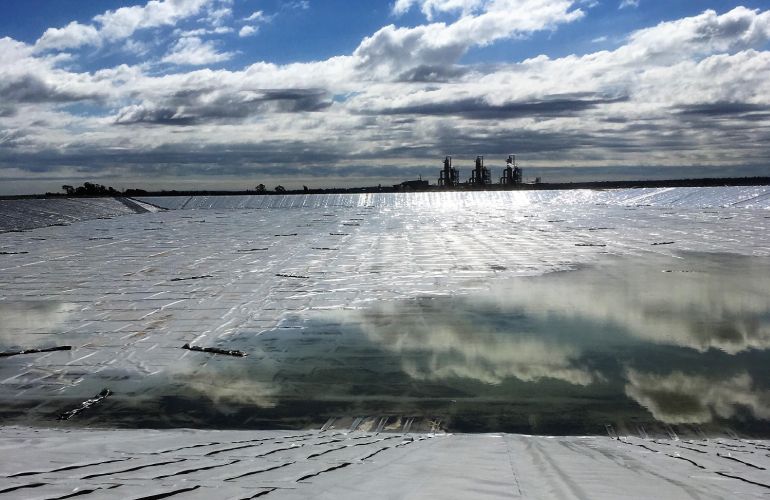
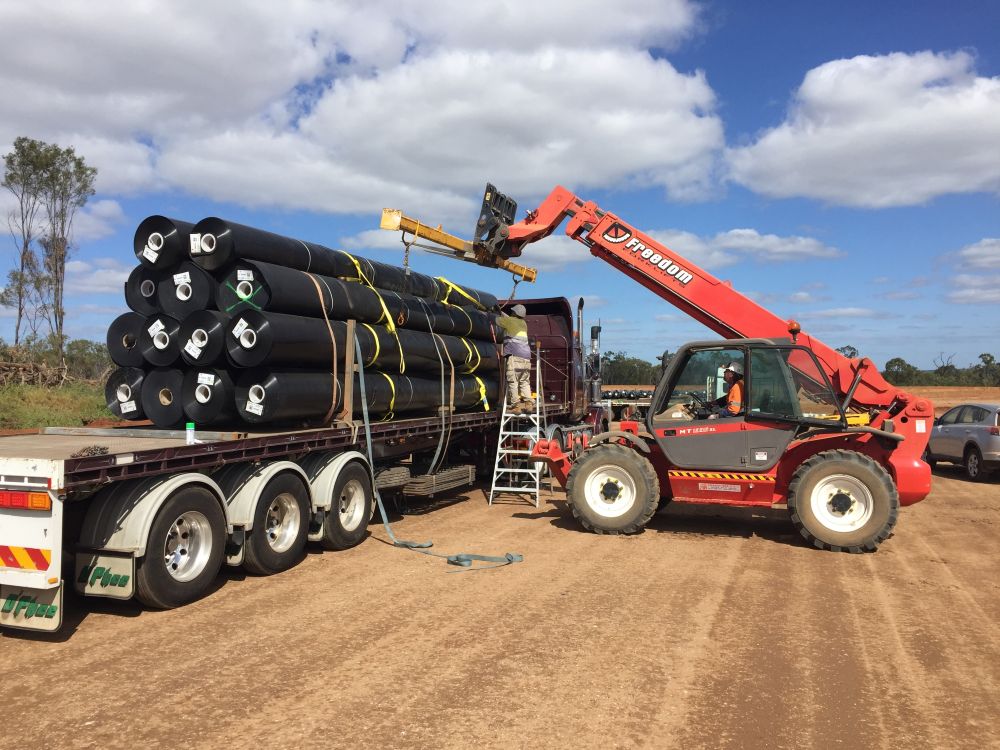
Geosynthetic Material Procurement
GeoQ leverages its expertise to offer impartial advice and support in the procurement of geosynthetic materials from top-tier international manufacturers, aligning product selection with the technical specifications of designers. Our services extend beyond consultation to encompass engineering support, logistics and contract management, ensuring that our clients receive materials that meet the highest industry standards. In addition, GeoQ meticulously calculates material quantities required for each project, factoring in wastage, overlaps and constructability issues unique to the design and installation methods employed, to guarantee efficiency and cost-effectiveness.
- We specialise in unbiased procurement of international geosynthetic materials.
- We offer comprehensive support services covering technical, engineering, logistics and contract administration.
- We precisely calculate material quantity to ensure cost-efficiency and align with project-specific requirements.